Evaluating key metrics
Redefining performance and other key metrics
Speed is only part of the story. We believe “speed” has become a confusing, poorly defined term in the 3D printing industry due to the many factors that can affect and change this. We find that performance and other metrics give you a more well-rounded understanding of what you’ll be getting from your printing platform.
What do we mean by high “performance”?
Let’s delve into how we define performance to better explain the superiority of UpNano’s offerings. Performance comprises of tolerance, measured by the Cp and Cpk value (process capability index), which determines the quality and yield of the printed parts, and throughput, determining the cycle time and thus the cost per piece.
1. Tolerance: within the context of 3D printed parts
Unparalleled tolerance is characteristic of the 2PP 3D printing method in general due to its ability for polymerization at such a precise focal point and cannot be matched by any other 3D print technology known today, including DLP, SLA, µSLA or FDM.
With the 5x objective in coarse mode, our highest throughput yet lowest resolution print mode, ten times higher tolerances (CP, CPk values) can be achieved compared to µSLA. Even tighter tolerances in the submicron range are achievable with our higher magnification and numeric aperture (NA) objectives. We balance speed and precision through our patented Adaptive Resolution across all of our objectives, which allows for higher throughput in bulk areas with our “coarse” mode and more precise details with our “fine” mode in more intricate areas. This method is available on all our printing platforms.
Process capability assesses whether a process meets a set specification. The process capability index or process capability ratio (Cpk) is a statistical measure that quantifies the ability of a process to produce output within specification limits. The capability of a process is then a function of two parameters:
- Repeatability: Compared to the width of the specification limits, measured by Cp
- Accuracy: Measured by bias
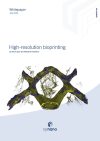
2PP 3D print technology allows for Six Sigma quality (even beyond Six Sigma in some cases) without additional cost.
1. Tolerance: within the context of 3D printed parts
Unparalleled tolerance is characteristic of the 2PP 3D printing method in general due to its ability for polymerization at such a precise focal point and cannot be matched by any other 3D print technology known today, including DLP, SLA, µSLA or FDM.
With the 5x objective in coarse mode, our highest throughput yet lowest resolution print mode, ten times higher tolerances (CP, CPk values) can be achieved compared to µSLA. Even tighter tolerances in the submicron range are achievable with our higher magnification and numeric aperture (NA) objectives. We balance speed and precision through our patented Adaptive Resolution across all of our objectives, which allows for higher throughput in bulk areas with our “coarse” mode and more precise details with our “fine” mode in more intricate areas. This method is available on all our printing platforms.
Process capability assesses whether a process meets a set specification. The process capability index or process capability ratio (Cpk) is a statistical measure that quantifies the ability of a process to produce output within specification limits. The capability of a process is then a function of two parameters:
- Repeatability: Compared to the width of the specification limits, measured by Cp
- Accuracy: Measured by bias
2PP 3D print technology allows for Six Sigma quality (even beyond Six Sigma in some cases) without additional cost.
2. Throughput: within the context of 3D printed parts
Throughput in 2PP is defined as mm3 print volume per hour. This is vital whether you’re using our NanoOne print systems or are determining the cost per printed piece with our NanoPro print service, affecting the economic efficiency of the process.
Multiple elements influence the efficacy of 2PP print processes and therefore the throughput, including the objective, the specific geometry, the part complexity and the selected software modules.
Determining factors of throughput and therefore the cost efficiency of a print process

1.6 Megavoxels/second (16 Bit)
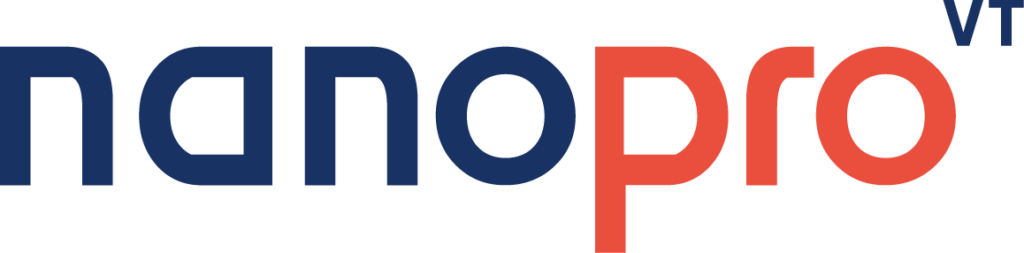
32 Megavoxels/second (16 Bit)
Elements that determine throughput
Megavoxels/second
The “Megavoxels/second” i.e. million volume pixels/second metric quantifies the basic underlying power of the respective print system.
Laser power
To print with the low magnification and low NA objectives (10x and 5x) high volume microparts, sufficient laser power is needed. Therefore, the NanoOne can be equipped with up to 1-watt femtosecond laser and the NanoPro VT operates with a 7-watt laser system enabling throughputs of several thousand mm3/h. The high throughput of the NanoOne platform on a prototyping scale and NanoPro VT on an industrial production scale both lead to optimized part cost.
Correlation between numeric aperture (NA), resolution (voxel size) and wavelength
The NA directly correlates with the voxel size (height as well as diameter). With our printers containing the 780 nm laser wavelength, a 60x objective with a NA of 1.5 voxel sizes of less than 500 nm in height and less than 200 nm in diameter can be achieved. In combination with adequate software algorithms allows for smallest feature sizes in the submicron range and optimal surface roughness but limited throughput. On the other hand, a 5x objective with NA 0.2 allows voxel sizes around 20 µm vertically and 1 µm in diameter, thus allowing much higher throughput but lower resolution.
A 780 nm laser wavelength (as used in some variants of the NanoOne) has a voxel size which is around 30% larger compared to a 515 nm wavelength (as used in the NanoOne Green and the NanoPro VT). Therefore, resolution is higher and the minimal feature size is 1/3 smaller with the NanoOne Green and the NanoPro VT.
Throughput versus feature size and tolerance
One of the most important considerations at the beginning of a process development is to balance the minimal requested feature size and tolerance expectation versus throughput and part cost. An optimal balance can be achieved in an iterative development process.
Additional benefits of our 2PP printing platforms
Precision, accuracy, feature size and surface roughness
A great advantage of using 2PP 3D print systems is the flexibility to use different magnification objectives with various NAs.
Precision and accuracy equal one voxel, which can be as small as 150 nm or below depending on the objective.
Resolution is the smallest feature size and can be as small as one voxel, typically a few voxels.
Surface roughness is the measure of small-scale features on a surface and therefore its quality. Our print-modi enables surface roughness below 10 nm, ideal for micro-optical applications and microfluidic products where low cell adhesion is desired.